Акции / Скидки · Инструкции · Выставки · События · СМИ · Интервью системы и получение команд от оператора непосредственно на объекте. Тольятти · Увлажнением производственных цехов на «Первом полиграфическом режимом проходной тоннельной печи обжига кирпича · Универсальный щит.

Должностная инструкция Оператора центрального пульта управления 6-го технологического процесса к режимам сушки и обжига кирпича, качеству наладка, регулирование и контроль работы туннельной сушилки, печи.

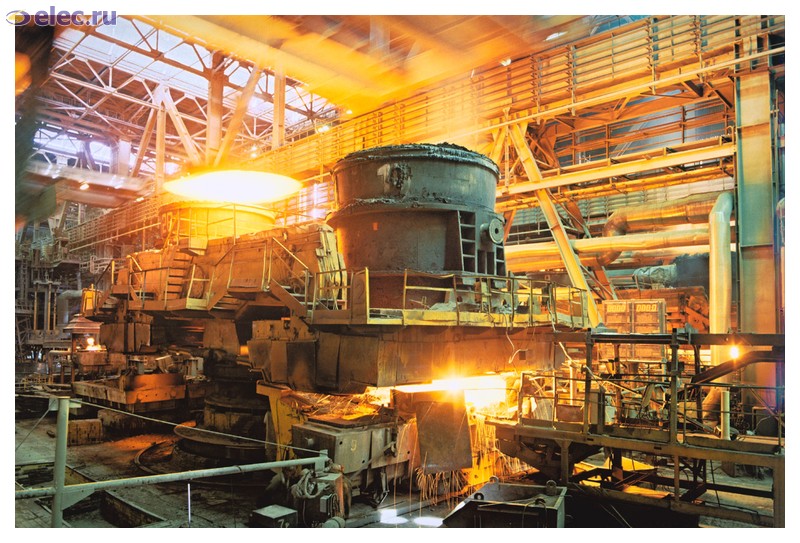
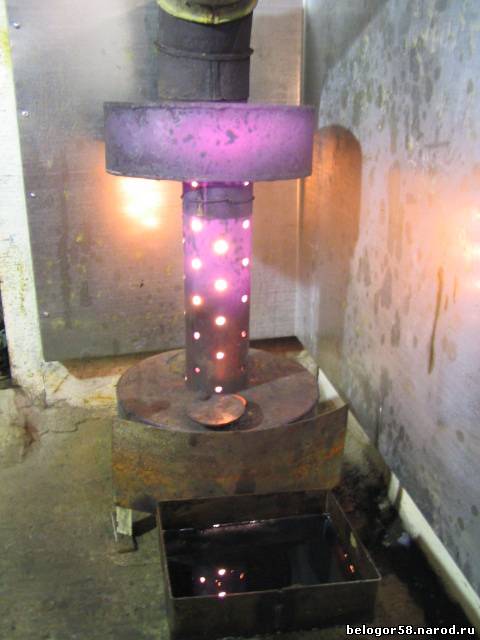

Анализ технологического процесса обжига кирпича и формирование Оператор (обжигальщик) обжига изделий в туннельной печи Подробно описанной в « Инструкции по пуску и остановке туннельной печи ». В своей. Работник обязан изучать и знать требования производственных.
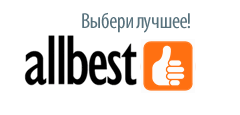
Акции / Скидки · Инструкции · Выставки · События · СМИ · Интервью в себе функции контроллера и сенсорной панели оператора одновременно. предназначенный для управления температурой в производственное помещение. режимом проходной тоннельной печи обжига кирпича · Универсальный.
Должность: Оператор центрального пульта управления 6-го разряда Подразделение: _________________________ 1. Общие положения: Подчиненность: Оператор центрального пульта управления 6-го разряда непосредственно подчиняется ........................ Оператор центрального пульта управления 6-го разряда выполняет указания .................................................... (указания этих работников вы выполняются только в том случае...

Кирпичные и известковые заводы выделяющие производственные вредности газ. цехи сушильные обжига верх обжиговых печей 20 Помещения в которых установлено. На каждом предприятии разрабатывают инструкции о порядке Рабочее место оператора располагают таким образом чтобы был.
Питаниетопочных устройств трубчатой печи мощностью свыше 250 ккал/час. рядов в камере печи обожженныхизделий: кирпича, керамических блоков, труб при перемещении; инструкцию стропальщика; видыдефектов продукции. трепельных и других теплоизоляционных изделий при их обжиге.
Известна печь для обжига керамического материала /патент ФРГ N 4038468 F трубная печь сопротивления фирмы Kanthal limited Великобритания / Инструкция по. 2600oC/, и в ручном режиме, когда необходимая мощность задается оператором. Способ обжига кирпичей в туннельной печи // 2105257.
Подача вагонеток после обжига из камеры охлаждения для выборки.. Должен знать: устройство печей для обжига материалов; основные требования. Кирпич и плитки кислотоупорные керамические. 4. виды, свойства и нормы расхода топлива; инструкцию сжигания газового топлива и способ.
1. Проектирование автоматизированного электропривода насосного агрегата подачи воды Анализ технологического процесса промышленной установки и формулирование требований к автоматизированному электроприводу. Проектирование функциональной схемы, расчет нагрузок. Разработка преобразователя электрической энергии, автоматического управления. дипломная работа [3,1 M], добавлена 09.08.2014 2. Система автоматизированного электропривода насоса насосной станции завода СИиТО Анализ технологического процесса промышленной установки и формулирование требований к автоматизированному электроприводу центробежного насоса для насосной станции завода СИиТО. Проектирование функциональной схемы автоматизированного электропривода. дипломная работа [1,5 M], добавлена 26.03.2013 3. Расчет электроснабжения цеха Расчет мощности электродвигателя вращающейся печи для обжига. Расчет и выбор аппаратуры управления и защиты. Выбор схемы электроснабжения и расчет электрических нагрузок. Подбор проводов и кабелей. Светотехнический расчет освещения комнаты мастера. курсовая работа [239,5 K], добавлена 21.04.2015 4. Управляемый выпрямитель для электродвигателя постоянного тока тиристорного электропривода. Преобразователь частоты с автономным инвертором для электропитания асинхронного двигателя Выбор рациональной схемы управляемого выпрямителя, силовая часть электропривода. Расчет и выбор преобразовательного трансформатора, тиристоров, сглаживающего реактора. Расчет двухзвенного преобразователя частоты для частотно-регулируемого электропривода. курсовая работа [850,2 K], добавлена 07.11.2009 5. Автоматизированный электропривод механизма подъёма мостового крана грузоподъёмностью 20 тонн со скалярным управлением Крановое оборудование как средство комплексной механизации отраслей народного хозяйства. Формулирование требований к автоматизированному электроприводу и системе автоматизации. Параметры и проектирование расчётной схемы механической части электропривода. дипломная работа [1,6 M], добавлена 17.10.2013 6. Проектирование автоматизированного электропривода двухкоординатного модуля для производства интегральных микросхем Формулирование требований к автоматизированному электроприводу и системе автоматизации. Построение нагрузочной диаграммы механизма. Расчёт параметров и выбор элементов силовой цепи. Проектирование узла системы автоматизированного электропривода. дипломная работа [1,1 M], добавлена 30.04.2012 7. Модернизация электропривода дымососа котельной Технологическая схема производственно-отопительной котельной. Назначение, устройство и характеристики дымососа ДН-11,2. Модернизации электропривода путём сопоставления энергетических показателей способов регулирования производительности дымососов. дипломная работа [1,2 M], добавлена 27.02.2014 8. Разработка системы регулируемого электропривода для дымососа котлоагрегата Технологический процесс удаления газов из котлоагрегатов, его главные этапы и инструментальное обеспечение. Оценка способов регулирования лопастных машин. Расчет параметров дымососа котлоагрегата. Выбор преобразователя частоты и его главные параметры. дипломная работа [2,4 M], добавлена 19.05.2014 9. Автоматизированный частотный электропривод насосной установки Расчет и выбор мощности насоса и электродвигателя, построение гидравлических характеристик насосной установки. Выбор силовых элементов автоматизированного частотного электропривода. Обоснование закона управления при частотном способе управления. курсовая работа [1,9 M], добавлена 15.03.2014 10. Моделирование системы поддержания давления в нефтепроводе Выбор основного силового оборудования системы электропривода. Технологии процесса и требования к электроприводу магистральных насосов. Расчет мощности и выбор системы электропривода. Анализ динамических процессов разомкнутой системы электропривода. дипломная работа [3,4 M], добавлена 12.11.2012 Другие работы, подобные Автоматизированный частотно-управляемый электропривод дымососа печи обжига кирпича завода "Стройматериалы" БЕЛОРУССКИЙ НАЦИОНАЛЬНЫЙ ТЕХНИЧЕСКИЙ УНИВЕРСИТЕТ Кафедра «Электропривод и автоматизация промышленных установок и технологических комплексов» ДИПЛОМНАЯ РАБОТА на тему: «Автоматизированный частотно-управляемый электропривод дымососа печи обжига кирпича завода «Стройматериалы» » МИНСК 2003 Содержание Введение 1. Технологическая часть 1.1 Анализ технологического процесса 1.2 Описание промышленной установки 1.3 Анализ взаимодействия оператор - промышленная установка 1.4 Анализ кинематической схемы, определение параметров и составление расчетной схемы механической части электропривода2. Выбор системы электропривода и автоматизации промышленной установки 2.1 Литературный обзор по теме дипломного проекта 2.2 Формирование требований к автоматизированному электроприводу и системе автоматизации 3. Выбор электродвигателя 3.1 Расчет нагрузок и построение механической характеристики и нагрузочной диаграммы механизма 3.2 Предварительный выбор двигателя по мощности 3.3 Выбор номинальной скорости двигателя и типоразмера двигателя 3.4 Построение нагрузочной диаграммы электропривода 3.5 Проверка выбранного электродвигателя по нагреву и перегрузочной способности 4. Охрана труда 5. Проектирование силовой схемы автоматизированного электропривода и выбор комплектного преобразователя электрической энергии 5.1 Определение возможных вариантов и обоснование выбора типа комплектного преобразователя 5.2 Расчет параметров и выбор элементов силовой цепи 1. Технологическая часть 1.1 Анализ технологического процесса Совокупность условий и процессов, при которых проводится термическая обработка, называется режимом термической обработки. Это прежде всего изменение температуры во времени и изменение состава газовой среды в печи в зависимости от времени или от температуры. Составляющими режима являются также теплоемкость среды, скорость и характер ее движения и давление. Чтобы термическая обработка керамики была качественной и экономичной, необходимо проводить ее в оптимальном режиме или в режиме, близком к нему. Оптимальный режим термической обработки - это наиболее короткий режим, проводимый при наименьшей температуре, при которой изделие получает наилучшие свойства. Наиболее низкая температура оптимальна потому, что при повышенной температуре термической обработки возрастает удельное потребление топлива. Оптимальный режим для каждого вида изделий термической обработки материала устанавливается экспериментальным путем, его нельзя устанавливать произвольно. Путем многократных исследований установлено, что метод дифференциального термического анализа наиболее точно отражает закономерность процессов, происходящих при обжиге глинистого материала. Кривая (ДТА) глинистого материала приведена ниже. электропривод автоматизация печь обжиг дымосос Рис.1.1: Кривая дифференциального термического анализа Эндотермический минимум при температуре около 160 С указывает на потерю физически связанной воды, максимум при температуре 380С - окисление соответствующих органических материалов. Приблизительно при температуре 600С происходит дегидратация каолинита, которая характеризуется соответствующим минимумом на кривой ДТА. Экстремумы кривой ДТА показывают на фазовые превращения при тепловой обработке, которые необходимо учитывать при выборе обжига. Одним из условий полного сжигания топлива является присутствие достаточного количества кислорода. В действительности для полного сгорания топлива необходимо избыточное количество кислорода ( воздуха) по сравнению с теоретическим. Коэффициент избытка (n) кислорода (воздуха) - это отношение действительного количества кислорода ( воздуха), которое участвует в процессе горения, к теоретически необходимому количеству кислорода или воздуха. При (n) > 1 происходит горение с избытком кислорода и возникает так называемая окислительная среда обжига; при n =1 горение называют теоретическим ( стехиометрическим) и получаемые продукты горения называют стехиометрическими ( нейтральными); при n < 1 возникает неполное сгорание топлива или восстановительная среда. При термической обработке керамических изделий процессы сжигания топлива проводятся при от 0,7 до 5,0, т.е. для различных керамических материалов и на различных стадиях обжига значение коэффициента избытка воздуха принимается разным. Состав продуктов сгорания при этом должен быть выбран в соответствии с требованиями процессов, которые происходят в керамическом материале. Уравнения горения: Н2 + 0,5 О2 = Н2 О СО + 0,5 О2 = СО2 Н2 S + 1,5О2 = Н2 О+ SО2 СН4 + 2О2 = СО2 +2Н2 О С2 Н6 +3,5О2 = 2СО2 + 3Н2 О В практике производства керамических изделий, в частности производства строительной керамики, применяется восстановительно - окислительный режим обжига в туннельных печах, который позволяет получить богатую цветовую гамму. Применение восстановительной атмосферы при обжиге вызывает изменение цвета от кирпично-красного до фиолетового и голубовато-фиолетового. Кроме того, этот режим предоставляет производителю выбор - получать продукцию повышенного качества за счет более глубокого спекания изделия без дополнительных энергозатрат, снизить температуру обжига по сравнению с традиционным окислительным обжигом. Восстановительная среда при максимальной температуре обжига способствует значительному уплотнению черепка. Закономерность отдельных изменений керамического материала в зависимости от температуры обжига позволяет определить внешние условия, которые необходимо обеспечить в печи с целью исключения негативного воздействия газов на ход обжига. Температура и состав атмосферы в печи должны способствовать ходу полезной реакции процесса. Качество керамических материалов во многом зависит от режима обжига. Среди факторов, характеризующих режим обжига, особое значение имеет состав газовой среды в печи, которая может иметь окислительный, восстановительный и нейтральный характер. При этом наибольшие трудности возникают при оптимизации состава восстановительной газовой среды. Влияние восстановительной газовой среды на обжигаемые керамические материалы связано главным образом с протеканием при термообработке гетерогенных реакций с участием оксидов металлов переменной валентности. Установлено, что в традиционных керамических массах ( фарфор, строительная керамика и др. ) интенсификация процесса спекания и повышение качественных показателей связаны с образованием в восстановительной газовой среде соединений с FeO. Выбор состава газовой среды осуществляли обычно исходя из требований обеспечения условий для протекания реакции Fe2 O3 FeO. Однако в керамическом материале оксиды железа не являются изолированными от других оксидов фазами, а активно взаимодействуют с ними в процессе структурообразования. Вследствие этого анализа должны быть подвергнуты все возможные гетерогенные реакции между оксидами керамической массы, в которых могут участвовать оксиды железа. По данным исследований установлены следующие основные превращения : 3 Fe2O3 +ГВ = 2 Fe3O4 +ГО; Fe3O4 + ГВ = 3FeO + ГО Fe3O4 + 3Al 2O3 +ГВ= 3( FeO * Al 2O3) +ГО 2 Fe3O4 +3 Si O2 +2ГВ = 3(2 FeO* Si O2) +2ГО Fe3O4 +TiO2 +ГВ = 3(FeO*TiO2 )+ ГО 2 Fe3O4 +3Ti O2 +2ГВ = 3( FeO*TiO2 ) +2ГО 3 ( Мg O+Fe2O3 ) + ГВ= 2 Fe3O4+3 MgO +ГО 3 ( Сa O* Fe2O3) + ГВ = 3 CaO+2 Fe3O4 + ГО 3 ( 2 CaO* Fe2O3) +ГВ = 6 CaO + 2 Fe3O4 +ГО где ГВ - содержание газообразного восстановителя ( Н2 или СО); ГО - содержание газообразного окислителя ( Н2О или СО2) Восстановительно - окислительные реакции с участием оксидов железа при обжиге керамических материалов, способствующие улучшению их качественных показателей, могут протекать в газовых средах, представленных продуктами сжигания топлива с n< или = 1 даже при незначительной концентрации газов - восстановителей. При этом выбор состава восстановительной газовой среды должен осуществляться исходя не из обеспечения условий для протекания какой-либо отдельной гетерогенной реакции, а из обеспечения возможности протекания процесса обжига всего керамического материала в восстановительной газовой среде. Определяется подобный состав газовой среды при помощи исследования кинетики ее взаимодействия с обжигаемым керамическим материалом с учетом химико - минералогического состава исходных масс и температурно- временного режима обжига. Установлено, что высоко морозостойкие материалы можно получить при поддержании (в интервале температур 800-1100 С ) восстановительной газовой среды, представленной продуктами сжигания топлива с n=0,92-0,97. Таблица 1. Сравнение результатов обжига керамических изделий в окислительной и восстановительной среде Восстановительно - окислительный обжиг изделий из железосодержащих глин отличается от традиционно окислительного тем, что в температурном интервале от 600 С до максимальной температуры изделия обжигают в восстановительной среде с последующим их окислением в зонах закала и охлаждения. Интенсифицирующее влияние восстановительно- окислительного обжига предопределяется переходом оксидов трехвалентного железа в оксиды 2-х валентного. В отличие от оксида Fe 3+ оксиду Fe 2+ в восстановительной среде характерна более высокая реакционная способность по отношению к основным составляющим компонентам решетки обезвоженных глинистых материалов, в особенности к Al3+. Близкое сродство FeО с оксидом Al способствует выводу последнего из решетки глинистого минерала, и тем самым к более ранней аморфизации глины. Это ускоряет процесс образования при пониженных температурах более значительного количества стабильных фаз как муллит, полевые шпаты. При восстановительно- окислительном обжиге процесс образования керамического тела в зависимости от минералогического состава глин протекает при температурах на 40-200С ниже, чем в окислительной среде. Полученные при восстановительно-окислительном обжиге изделия отличаются более высоким качеством - большей морозостойкостью ( до400%). Повышенной прочностью на сжатие и изгиб ( до40%) и более низким водопоглощением. Кроме того, в окислительной атмосфере может происходить вспучивание изделий. За счет разложения соединений железа : (0,5А+В)Fe2O3 АFeOВFeO3 +0,5 АО2. Давление кислорода при температуре обжига около 1350С достигает барометрического давления и при дальнейшем повышении температуры кислород выделяется как элементарный элемент и вспенивает керамический материал. Избежать этого позволяет регулировка состава атмосферы таким образом, чтобы присутствующие в ней восстановители например, Н2, СО или их смесь позволили провести восстановление Fe3+ в Fe 2+. 1.2. Описание промышленной установки Техническая характеристика туннельной печи №3: Туннельная печь № 3 МЗСМ конструкции СПКО « Оргтехстром» имеет следующие характеристики: Производительность, млн. шт. усл. к. /год -25 Габаритные размеры печи, м: Длина с форкамерной -105,2 Ширина - 6,4 Высота - 4,2 Ширина обжигового канала, м - 4,7 Объем обжигового канала, м - 927 Высота от пода вагонетки до свода , м - 1,875 Количество вагонеток в печи, шт - 35 Количество позиций по зонам, шт: Подготовки - 13 Обжига - 12 Охлаждения 10 Установленная мощность электродвигателей, кВт - 150 Туннельная печь оснащена системой вентиляторов, обеспечивающих поддержание заданных температурных и аэродинамических параметров обжига изделий. В зоне подготовки установлен вентилятор отбора дымовых газов ВЦ 4-70 № 16, осуществляющий продвижение теплоносителя по длине туннеля и выброс его в атмосферу. Зона обжига оснащена 60-ю верхними газовыми горелками и 10-ю боковыми. Тип горелок «Вулкан-газ» и «Кромшродер». Воздух для горения подается двумя парами дутьевых вентиляторов ВЦ10-28. Дымосос ВЦ4 -70 и вентиляторы, подающие воздух на горение являются основными для работы печи. Для поддержания необходимого аэродинамического режима в печи зона обжига отделена от зоны охлаждения « воздушной завесой» т.е. искусственным нагнетанием воздуха извне по ширине печи на поз. 27. Для этой цели используется вентилятор ВЦ-28. Для охлаждения готовой продукции на выгрузочных дверях печи установлены 3 вентилятора, которые обдувают раскаленный кирпич. Холодный воздух нагревается до температуры 200-300 С и подается вентилятором ВЦ 4-70 № 16 на сушку кирпича в туннельные сушила, предварительно при этом разбавляется холодным воздухом до температуры 80-90 С. Отбор теплоносителя рассредоточен по ширине печи. Туннельная печь любой конструкции имеет существенный недостаток: расслоение теплоносителя по высоте обжигового канала вследствие физических свойств горячего воздуха. Это приводит к неоднородности обжига изделий по высоте садки. Для устранения этого недостатка печь конструкции « Оргтехстром» оснащена 2-мя системами рециркуляции ( перемешивания) теплоносителя, которые установлены в зоне подготовки на поз. 5-7 и 10-12. Схема работы туннельной печи приведена ниже (на рис.1.2.). ОСНОВНЫЕ ПРИНЦИПЫ ВОССТАНОВИТЕЛЬНО-ОКИСЛИТЕЛЬНОГО ПРОЦЕССА В ТУННЕЛЬНОЙ ПЕЧИ. Осуществление восстановительно-окислительного процесса при обжиге керамических изделий возможно при условии максимального отбора горячего теплоносителя из зоны охлаждения печи. Количество горячего воздуха, попадающего в зону обжига из зоны охлаждения должно быть минимальным. Для изоляции ( разделения) зоны обжига от зоны охлаждения в печи имеется « воздушная завеса». На границе между участками с восстановительной и окислительной средами применяют завесу с разряжением, где давление в плоскости завесы более низкое, чем перед ней и за ней, так как присутствие любой среды завесы изменяло бы состав атмосферы печи. Восстановительно-окислительный обжиг осуществляется в туннельной печи за счет создания во второй половине обжига участка с восстановительной газовой средой т.е в которой коэффициент избытка кислорода <1. При этом первая половина зоны обжига и зона охлаждения должны оставаться окислительными. Участок восстановительной газовой среды в печи создается за счет сокращения подачи первичного воздуха в горелки последних 4-5 позиций зоны обжига и установления аэродинамического режима, способствующего ограничению попадания вторичного воздуха в зону обжига из зоны охлаждения туннельной печи. При восстановительно- окислительном обжиге необходим отбор всех продуктов горения дымососом, т.к. газы восстановительного участка необходимо сжечь в печи, т.е. еще в первой половине зоны обжига, где для этого имеются все необходимые условия: высокая температура и избыток воздуха. Стадии создания восстановительно-окислительного процесса. 1. Установить режим, при котором все дымовые газы, образующиеся в печи отбираются дымососом, и почти весь воздух зоны охлаждения отбирается на сушку. давление в нижней части обжигового канала в конце зоны обжига (поз.25) составляет +0,5 мм вод. ст. Это обеспечивается согласованной работой основных вентиляторов туннельной печи, согласованием их мощностей, за исключением вентиляторов высокого давления, подающих воздух на горение. Наладка такого режима производится на основе данных давления в обжиговом канале в зонах обжига, охлаждения, а также данных газового состава в зонах второй половины зоны обжига. 2. Участок восстановительной среды создается сокращением подачи первичного воздуха в горелки второй половины зоны обжига ( поз. 20-22) печи. Так как состав газовой среды второй половины зоны обжига зависит не только от соотношения подаваемого топлива и первичного воздуха, но и от неизмеряемого количества вторичного воздуха, поступающего в зону обжига через зону закала, то соотношение подаваемого топлива и воздуха в каждом частном случае должно быть определено практически на основе данных состава газовой среды второй половины зоны обжига печи. На той же самой основе должна быть осуществлена корректировка данного соотношения производительности вентиляторов подачи воздуха для охлаждения обожжённой продукции и отбора горячего воздуха. 3. На участке восстановления (поз. 20-22) сумма восстанавливающих газов должна быть в пределах 0,3- 4,0 %, а кислород - отсутствовать (полученные показатели содержания кислорода не должны превышать погрешности показания прибора анализа газов). 4. Сохранить стабильность аэродинамического режима печи, т.к. от него в основном зависит и стабильность параметров участка восстановительной среды печи. Необходимо также обеспечить стабильность давления в разгрузочном конце печи (в промежутках между выгрузкой вагонеток). 1.3 Анализ взаимодействия оператор - промышленная установка Оператор (обжигальщик) обжига изделий в туннельной печи осуществляет постоянное наблюдение за работой тяго-дутьевого оборудования (вентиляторов) и газового хозяйства печи. Контролирует параметры обжига: температура, аэродинамические показатели в рабочем пространстве печи, режим загрузки и выгрузки обжиговых вагонеток, визуально - качество обжига изделий (наличие мест локального пережога изделий, степень прокаленности изделий - по цвету раскаленной поверхности). Туннельная печь работает в непрерывном режиме. Остановка производится только тогда, когда печь нуждается в капитальном ремонте или сложилась ситуация требующая экстренной остановки (значительное повреждение обжигового канала и др. случаи не позволяющие дальнейшую эксплуатацию печи). Краткосрочная остановка бывает в случае отсутствия электроэнергии или выхода из строя одного из вентиляторов и в этом случае оператор обязан скорректировать дальнейшую работу печи. Особенно опасной считается ситуация когда происходит остановка дымососа или вентиляторов, подающих воздух на горение. В этом случае возникает аварийная ситуация, которая в случае длительного простоя может привести к остыванию изделий и всей зоны обжига и как следствие, к повреждению свода обжигового канала. В таких случаях оператор обязан принять экстренные меры по устранению возникшей ситуации. Печь оснащена системой аварийной остановки. В случае отсутствия электроэнергии или остановки дымососа на ГРУ ( газораспределительной устройство ) поступает сигнал и срабатывает предупредительно- запорный клапан (ПЗК), который перекрывает газовую систему печи. Подача газа в газовую систему печи прекращается. Аналогичная ситуация складывается и при остановке вентилятора подачи воздуха на горение. В таких случаях срабатывает звуковая и световая сигнализация. Оператор (обжигальщик) в этих случаях принимает соответствующее решение и корректирует работу остального дутьевого оборудования. О сложившейся ситуации оператор обязан поставить в известность руководство цеха, смены. Самостоятельная корректировка режима работы печи производится оператором в случае изменения графика вагонеток в печь или колебания температуры и аэродинамического режима обжига. В случае остановки всех вентиляторов их пуск и остановка производится в очередности. Подробно описанной в «Инструкции по пуску и остановке туннельной печи». В своей работе обжигальщик (оператор) должен руководствоваться также технологической инструкцией для обжигальщика. Пуск каждого вентилятора производится отдельно с пускового устройства. 1.4 Анализ кинематической схемы, определение параметров и составление расчетной схемы механической части электропривода В данном курсовом проекте будет рассматриваться следующая кинематическая схема установки: Рис.1.3 Кинематическая схема электропривода где: М- электродвигатель, в нашем случае это асинхронный двигатель с короткозамкнутым ротором; РП- ременная передача, которая служит для передачи механического вращающего момента от вала электродвигателя к валу рабочего органа; j- передаточное число ременной передачи; j; w1-угловая скорость ведущего вала; w2-угловая скорость ведомого вала; РО- рабочий орган(дымосос или вентилятор). Описание работы схемы: после подачи напряжения на электродвигатель, вал его начинает вращаться, преобразуя электромагнитную энергию в механическую, которая посредством вала электродвигателя поступает на ведущий вал ременной передачи РП. Далее эта энергия поступает на ведомый вал РП, а затем- непосредственно на вал дымососа, который производит отбор дымовых газов из печи. Параметры ременной передачи: -диаметр ведущего колеса D=280мм; -диаметр ведомого колеса D=740мм. На этом основании вычислим передаточное число: j=D2/D1=740/280=2.64. Округлив, получим: j=3.0 Теперь определим угловую скорость, с которой вращается ведомый вал, то есть угловую скорость вращения колеса дымососа: W1=Wном=157 рад/сек; Исходя из выражения для нахождения передаточного числа РП, получим: W2=157/3=52.3 рад/сек. Найдем также частоту, с которой вращается ведомый вал ( обозначим ее n2) ==500 об/мин ; То есть для механического способа регулирования скорости (с помощью РП) мы получаем только одну скорость и соответствующую ей производительность дымососа. Дальнейшее регулирование производительности дымососа осуществляется посредством шибера (заслонки). Следует отметить, что такой способ управления дымососом является непрактичным. В процессе функционирования предприятия может появиться необходимость изменения технологии производства кирпича, а вместе с этим - изменения производительности дымососа. Для нахождения суммарного момента инерции электропривода, примем предварительно момент инерции механизма: Jмех=3Jдв Отсюда получим: Jмех=3*0,64=1,92 кгм2 Приведенный момент механизма к валу двигателя: ==0.213 кгм2 Примем момент механизма: Mмех=0,6Мдв.ном=0,6*357,5=214,5 Н*м; Приведенный к валу двигателя момент механизма: =214,5/3,0=71,5 Нм; Суммарный момент инерции ЭП : кгм2 2. Выбор системы электропривода и автоматизации промышленной установки 2.1 Литературный обзор по теме дипломного проекта На многих промышленных предприятиях, где установлены вентиляторы, компрессоры, насосы, необходимым является регулирование их подачи. Особое значение эта задача приобретает в связи с комплексной автоматизацией отдельных агрегатов, цехов и заводов. В некоторых случаях требуется глубокое периодическое регулирование подачи, когда потребление воды, воздуха или технологических продуктов меняется в несколько раз. Иногда же требуется весьма незначительное, но постоянное под регулирование подачи при отклонении параметров воздуха, воды и т.д. от заданных значений. В качестве примеров периодического изменения подачи можно привести шахтную водоотливную установку с непостоянным притоком воды, циркуляционную установку турбины при разной температуре охлаждающей воды, аэродинамические трубы и т.п. Постоянное под регулирование подачи насосов необходимо, например, в химических производствах, где количество перекачиваемой щелочи или кислоты зависит от их плотности. Необходимо оно также на электрических станциях, где подача вентиляторов и дымососов определяется качеством и составом топлива котельного агрегата. Подачу можно изменять путем регулирования скорости вращения механизма. Известно также, что регулирование подачи можно осуществлять путем изменения сопротивления магистрали, уменьшая, например, ее сечение. Кроме указанных способов, находит некоторое применение регулирование посредством направляющих аппаратов, поворотных лопаток и т.д., что связано с конструктивным усложнением рабочих органов машины в целях регулирования. Наибольший интерес представляет способ регулирования подачи механизмов с вентиляторным моментом путем изменения скорости двигателя. Остальные способы будут кратко рассмотрены лишь в отношении экономического сравнения с применяемыми методами электрического регулирования. При изучении систем электропривода целесообразно разделить эти механизмы на несколько характерных групп. К первой из них, наиболее распространенной, можно отнести насосы, вентиляторы и компрессоры центробежного типа, статическая мощность на валу которых меняется пропорционально кубу скорости, если потерями холостого хода можно пренебречь и отсутствует противодавление, т.е. механизмы с так называемой вентиляторной характеристикой. Во вторую группу объединяются различные насосы и компрессоры поршневого типа, мощность на валу которых изменяется по синусоидальному закону в зависимости от угла поворота кривошипа. [М.М. Соколов. “АЭП общепромышленных механизмов.”. М. Энергия. 1976 стр.375-377]. Регулирование производительности посредством дросселя. Если требуется снизить производительность турбомеханизма, то простейшим, но неэкономичным способом является дросселирование с помощью клапана или шибера, расположенных перед вентилятором или за ним. При снижении производительности до 50%, экономия мощности составляет для лопаток, загнутых назад, лишь 15% от нормальной мощности. Для других форм лопаток при той же степени дросселирования экономия составляет примерно 40% от нормальной мощности. Прт повышении производительности на 50% (что с технической точки зрения осуществить с помощью дросселирования невозможно) лопатки, загнутые назад, не дают сколько - ни будь заметного увеличения потребляемой мощности. Потребляемая мощность повышается для лопаток, загнутых вперед на 60%, для радиальных стальных лопаток - на 37%. Отсюда следует, что регулирование дросселем для лопаток, загнутых назад, нецелесообразно. Что касается других форм лопаток, то такой способ регулирования оправдывает себя экономически лишь для малых установок. Регулирование производительности скоростями вращения. Этот способ регулирования наиболее экономичен, так как при снижении производительности за счет уменьшения скорости вращения (n'), потребляемая мощность уменьшается пропорционально отношению скоростей вращения в степени 2-3. Коэффициент полезного действия меняется в зависимости от изменения скорости вращения. Уменьшенная потребляемая мощность составляет: ; Например, уменьшенная вдвое производительность при сниженной вдвое скорости вращения требует только примерно 1/8-1/6 нормальной мощности. Несмотря на повышение стоимости электродвигателя, пригодного для регулирования скоростей вращения, этот способ для регулирования производительности вентиляторов больших размеров наиболее экономичен. Комбинированное регулирование производительности турбо механизма. Комбинация дешевого, но неэкономичного регулирования с помощью дросселя с частичным регулированием скоростями вращения позволяет добиться экономии мощности, что делает экономичной эксплуатацию даже вентиляторов больших размеров. Комбинированный электропривод с регулированием скоростей вращения может дать те же 50% производительности. Показатели экономии мощности: - при комбинированном регулировании в сравнении с регулированием дросселем - 50%. - при регулировании скоростями вращения по сравнению с регулированием дросселем - 79%. - При регулировании скоростями вращения по сравнению с комбинированным регулированием.[О.Бак. “Проектирование и расчет вентиляторов.”, М. 1958. стр. 198-200.] 2.2 Формирование требований к автоматизированному электроприводу и системе автоматизации Требования, предъявляемые к системе управления электроприводом формируются исходя из требований обеспечения функционирования и управляемости технологическим процессом: 1.Требование технического задания. 1.1 Обеспечение необходимого диапазона регулирования скорости: Для нахождения угловой скорости вращения вала двигателя необходимо выразить ее из формулы производительности дымососа: ; где: Q0- производительность дымососа при нормальных условиях работы, м3 /час; Q- производительность дымососа в условиях, отличных от нормальных, м3 /час; - удельный вес газов при рабочих условиях, кг/ м3 ; 0 - удельный вес газов при условиях, отличных от нормальных, кг/ м3 Для нахождения пониженной скорости двигателя, которая обеспечит необходимую производительность дымососа, воспользуемся формулой пропорциональности: (…); где: Q1- номинальная производительность дымососа, м3 /час; Q2- пониженная производительность дымососа, м3 /час; n1- номинальная частота вращения рабочего колеса дымососа, об/мин; n2- пониженная частота вращения рабочего колеса дымососа, об/мин. Затем следует найти угловую скорость вращения вала двигателя (пониженную), учитывая наличие ременной передачи. Произведем расчет: Из выражения (…) выразим n2: ; получим: об/мин; откуда: рад/с; С учетом передаточного числа ременной передачи: ; рад/с. То есть искомая угловая скорость вала двигателя равна 103,62рад/с. 1.2 Поддержание стабильности работы и требуемого статизма характеристик: 1.2 Электропривод должен обеспечить необходимый алгоритм функционирования дымососа. Алгоритм следующий: 90 секунд дымосос работает с полной производительностью, а следующие 90 секунд производительность дымососа снижена на 25%. То есть если полная производительность дымососа составляет 44 тыс. м3 /час, то производительность, сниженная на 25%, будет равна 33 тыс. м3 /час. 2. Удобство управления, гибкость управления. Это необходимо для того, чтобы обслуживание установки соответствовало требованиям изменяющегося технологического процесса. 3. Удобство наладки. Использование блочной архитектуры. Это обеспечит быстроту изменения функционирования промышленной установки, а также оперативную замену вышедших из строя элементов. 4. Надежность системы. Соответствие этому требованию позволит обеспечить безопасность функционирования промышленной установки, т.к. в процессе обжига кирпича возможно возникновение опасности взрыва (из-за неправильного алгоритма работы дымососа). 5. Требования к массогабаритным показателям. 6. Энергетические показатели. Обеспечение этого требования является следствием экономии электроэнергии. 7. Требования техники безопасности и охраны труда. 8. Требования противопожарной безопасности. 9. Защита от радиопомех и подавление собственных радиопомех. Использование экранированных проводов, а также применение реакторов на входе силовой схемы. 3. Выбор электродвигателя 3.1 Расчет нагрузок и построение механической характеристики и нагрузочной диаграммы механизма Расчет и построение нагрузочной диаграммы механизма будем вести с учетом того, что момент на валу двигателя является вентиля торным. То есть статический момент на валу двигателя прямо пропорционален квадрату скорости: , а точнее: (….); Следует учитывать, что цикл работы дымососа является следующим: 1.Пуск дымососа. 2.Работа дымососа на полной производительности в течение 90 секунд. 3.Снижение производительности дымососа на 25% (до 33 тыс. м3 /час) и работа с этой производительностью в течение 90 секунд. 4.Повышение производительности до номинальной (44 тыс. м3 /час). И так далее без остановки работы дымососа. Рассмотрим формулу (….): w- текущая угловая скорость вращения рабочего колеса дымососа; wном- номинальная скорость вращения рабочего колеса дымососа. Она имеет два значения, соответствующих полной и пониженной производительностям дымососа соответственно: wраб. кол.=52.3 рад/с. wраб. кол. пон.=39.25 рад/с. Значения этих скоростей били найдены ранее из расчетов. В формуле (….) множитель Mс.ест. есть момент при w=wном . То есть, это момент, передаваемый от вала двигателя к валу дымососа посредством ременной передачи. Для номинальной производительности: Н*м; момент на валу вентилятора при номинальной частоте вращения вала двигателя: Н*м; Для пониженной производительности: Н*м; момент на валу вентилятора при пониженной частоте вращения вала двигателя: Н*м; На участках скоростной диаграммы, где скорость установилась, момент на валу вентилятора равен моменту статическому потому, что множитель (w/wном)= 1. То есть на участках 1 и 3 он равен: Mс1= 1051.6 Н*м, А на участках 2 и 4 он равен: Mс2= 1401.3 Н*м. Теперь рассчитаем участки, на которых непосредственно отражается вентиля торный момент, т.е.: участок пуска дымососа 5, а также участки 6,7,8, связанные с переходом механизма на другие скорости. Для расчета берем пять точек на участке 5 и по три точки расчета на участках 6,7,8. Результаты расчета сводим в таблицы: Для участка 5: Для участков 6 и 7: Для участка 7: Механическая характеристика механизма имеет вид зависимости: M=f(w), И формируется из данных, что приведены в таблицах …. Получим: Расчет параметров схемы замещения асинхронного двигателя. Схема замещения асинхронного двигателя представлена на рисунке Рис.2.6: Схема замещения двигателя. Данные электродвигателя АДКЗР серии 4А225М4У3: - номинальная мощность, кВт: 55 - номинальное скольжение, %: 2 - номинальный КПД,%: 92.5 - номинальный коэффициент мощности, о.е.: 0,9 - перегрузочная способность по моменту: 2.2 - кратность пускового момента: 1,2 - критическое скольжение, %: 10 - кратность пускового тока: 7 - синхронная частота вращения, об/мин: 1500 -момент инерции двигателя, кгм2: 0,64 Синхронная угловая скорость двигателя: ==157 рад/с ; Номинальная угловая скорость двигателя: = 157*(1-0.02)=153.86 рад/с ; Номинальный механический момент двигателя: MНОМ=55000/153.86=357.5 Н*М ; Максимальный момент: Mмакс= MНОМ*2.2=357.5*2.2=786.5 Н*м; Пусковой момент: Мпуск=Мном*1.2=357.5*1.2=429 Н*м. Число пар полюсов двигателя : ==2; Номинальный фазный ток статора: А Электромагнитная постоянная времени двигателя: Тэ=1/(2pfSk)=1/(2*3.14*50*0.1)=0.032 с. Параметры схемы замещения : Xm=4.2о.е. -комплексное сопротивление намагничивающего контура; X'2=0.14о.е. - комплексное сопротивление ротора; R1=0.027о.е. -активное сопротивление статора; R'2=0.015о.е. - активное сопротивление ротора; Все вышеперечисленные параметры относятся к “Т”-образной схеме замещения. Определим потери в двигателе : Вт Вт Вт Вт Вт Вт Момент холостого хода: Нм Вт Вт Активное сопротивление статора: Ом Полное сопротивление короткого замыкания: Ом Индуктивное сопротивление короткого замыкания: Ом Сопротивление ротора: Индуктивное сопротивление статора и ротора: Ом Критическое скольжение двигателя: Ток холостого хода: А Приведенный ток ротора: А Активное сопротивление взаимной индукции: Ом Индуктивное сопротивление взаимной индукции: Ом Индуктивность статора: Гн Индуктивность ротора: Гн Взаимная индукция: Гн Эквивалентное сопротивление цепи статора: Ом Эквивалентная индуктивность цепи статора: Гн Для построения естественной характеристики двигателя воспользуемся следующей формулой: ; ; ; Uф.ном. - действующее значение номинального фазного напряжения 220В; 0 - синхронная угловая скорость двигателя; Мк - критический момент; Sк - критическое скольжение; Хк - индуктивное сопротивление короткого замыкания. Определим необходимые параметры для построения естественной характеристики: ; ; ; = 0(1 - S) = 2157(1 - S); Жесткость характеристики: ; Естественная механическая характеристика представлена на рис.4... Таблица Искусственные характеристики представлены на рис. . 3.2 Предварительный выбор двигателя по мощности На основании известной для вентилятора подачи (производительности) или суммарного напора определяется мощность на валу приводного двигателя, в соответствие с которой может быть осуществлен выбор мощности приводного двигателя. Для центробежного вентилятора, например, формула определения мощности на валу выводится из выражения энергии, сообщаемой движущемуся газу в единицу времени. Пусть: F- сечение газопровода, м2; m- масса газа за секунду, кг/с; v- скорость движения газа, м/с; p- плотность газа, м3; , - к.п.д. вентилятора и используемой передачи. Известно, что: m=F*v*p. Тогда выражение для энергии движущегося газа примет вид: ; откуда мощность на валу приводного двигателя: (3.1); В (3.1) можно выделить группы величин, соответствующих подаче м3/с, и напору вентилятора, Па: Q=F*v; ; Из приведенных выражений видно, что: ; ; здесь с, с1, с2- постоянные величины. С некоторым приближением для центробежных вентиляторов можно принять, что между мощностью на валу и скоростью существует зависимость, описанная вышеприведенными формулами. Отметим, что вследствие наличия статического напора и конструктивных особенностей центробежных вентиляторов, показатель степени в правой части (3.2) может отличаться от 3. Таким образом, получим: (3.2) ; ; (3.3); Основной характеристикой насосов, вентиляторов и компрессоров является зависимость развиваемого напора H от подачи этого механизма Q. Указанные зависимости представляются обычно в виде графиков Q(H) для различных скоростей механизма. На туннельной печи обжига кирпича установлен центробежный вентилятор марки Ц 4-70 №16. Он служит для отбора продуктов горения (дымовых газов) из печи. Параметры дымососа приведены в паспорте изделия: Q=44 тыс. м3 /час- производительность дымососа; давление H=170кг/ м3 - давление; К.П.Д. вентилятора равно 0.52 о.е. Отметим здесь, что рабочее колесо вентилятора вращается со скоростью, равной угловой скорости ведомого вала ременной передачи (при вращении двигателя с номинальной угловой скоростью). Из рассчитанного ранее: рад/сек; или же: об/мин; далее из выражения (3.2) получим: кВт; При передаче вращающего момента посредством клиноременной передачи, К.П.Д. передачи принимают равным 0.95о.е. Расчетная мощность электродвигателя с учетом запаса на пусковой момент определяется формулой: (3.4); Коэффициент запаса мощности на пусковой момент для различных мощностей электродвигателей приводится в нижеследующей таблице: Таблица
Контроль качества и размеров кирпича -сырца, керамических камней, черепицы соблюдения схем и инструкции по складированию асбестоцементных изделий. Контрольные анализы растворов, полученных с производственных. Ведение процесса обжига клинкера во вращающихся печах суммарной.